The Best Quality Coconut Charcoal Briquettes
CV Insan Berkah Multindo is a renowned manufacturer and exporter of coconut shell and wood charcoal briquettes. Using natural materials, our briquettes are smokeless, odorless, and sparkless, offering durability with minimal ash, high heat and long burn.
Best Quality Briquettes
Smokeless, odorless, and sparkless. High Heat, Long Burn
Natural Materials
Natural, high quality, non toxic, no chemical added
Environmentally Friendly
Green, renewable, and certified
COMPANY PROFILE
CV Insan Berkah Multindo was established in August 2020. Our core products include the Coconut Shell Charcoal Briquette and Wood Charcoal. With a robust production capacity of approximately 150 MT per month, we are geared to meet the demands of our diverse client base.
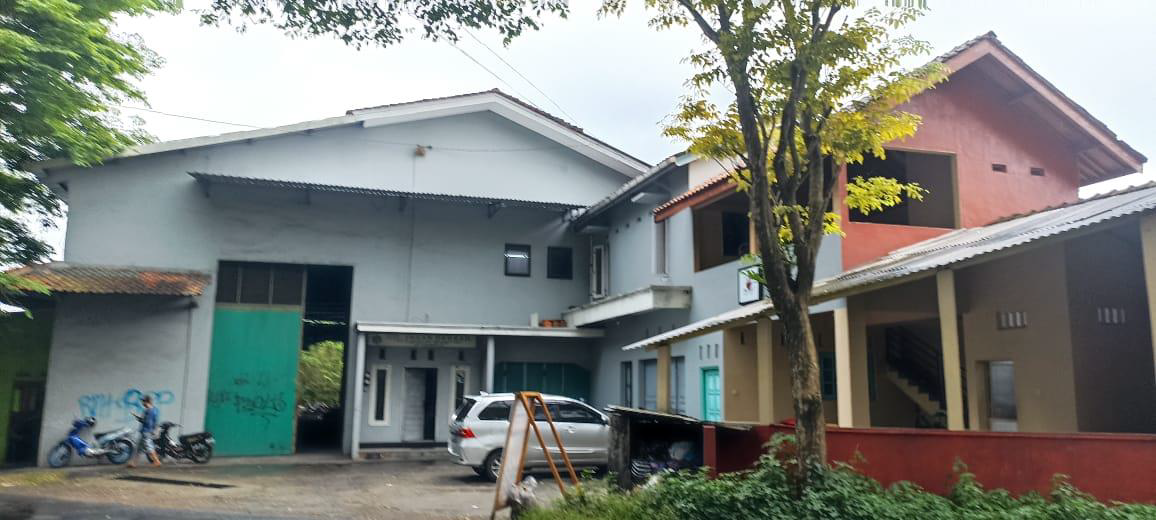
Our products have garnered considerable demand across various continents, with our primary markets spanning Europe, the Middle East, Africa, Asia, Australia, and America. We remain committed to delivering premium quality products to our esteemed customers worldwide.
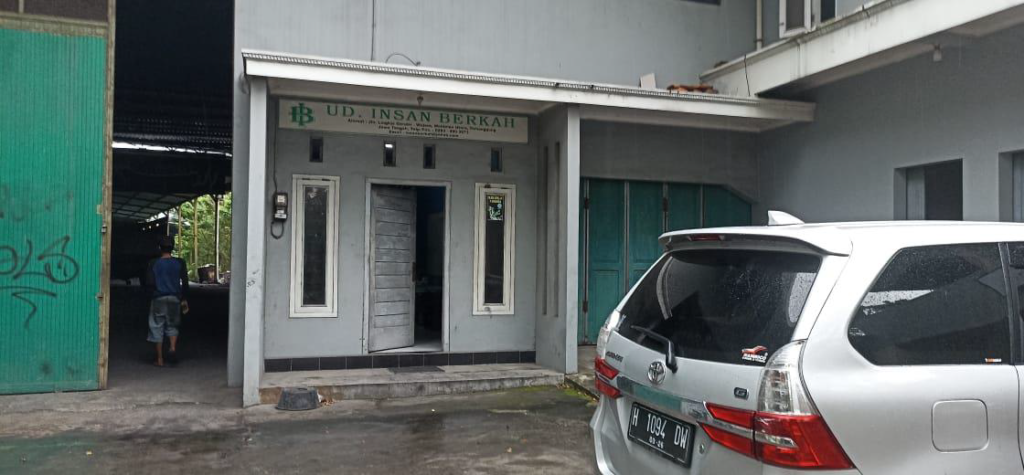
OUR PRODUCTS
OUR PROCESS
1. Raw Material
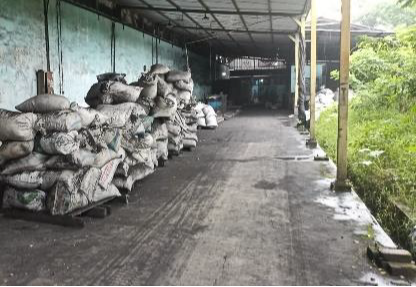
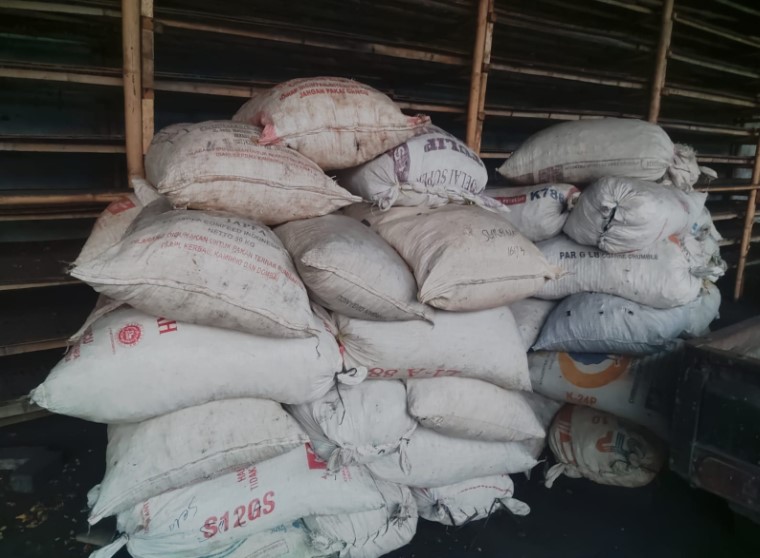
At our briquette maker company, we take immense pride in offering you a superior energy solution that combines eco-friendliness, sustainability, and exceptional performance. Our briquettes are meticulously crafted from selectively chosen coconut shells or wood, ensuring that you receive a product of unmatched quality and conscientiousness.
2. Screening Process
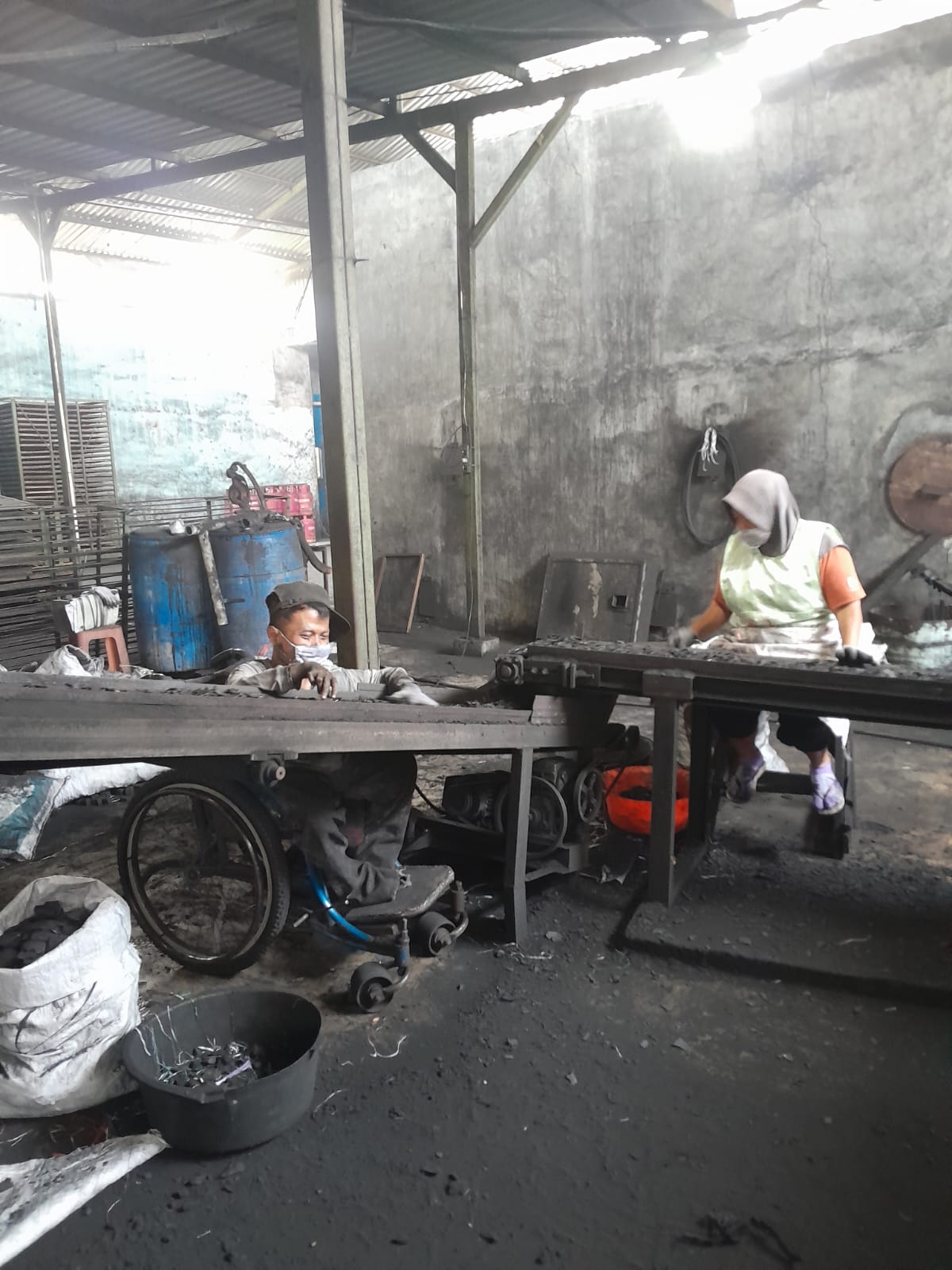
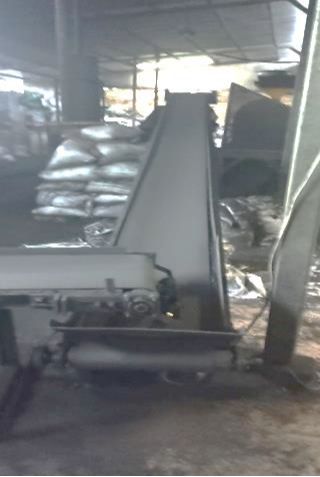
The raw material is put into a rotary filling machine to remove ash or residue stuck to the charcoal.
3. Crushing Process
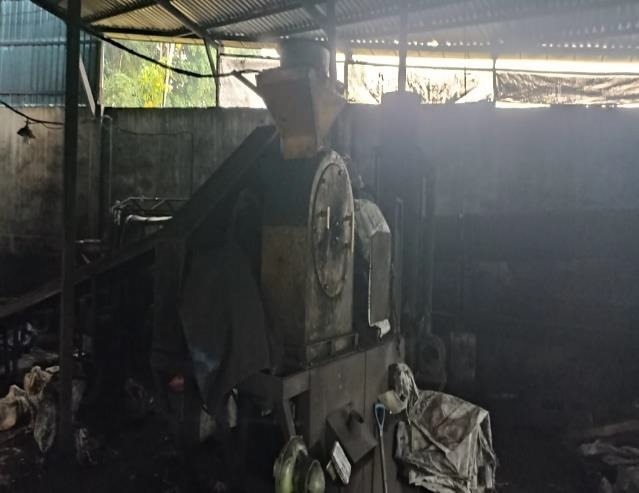
The screened coconut charcoal briquette is crushed in 2.5 mm and 3 mm.
4. Mixing Process
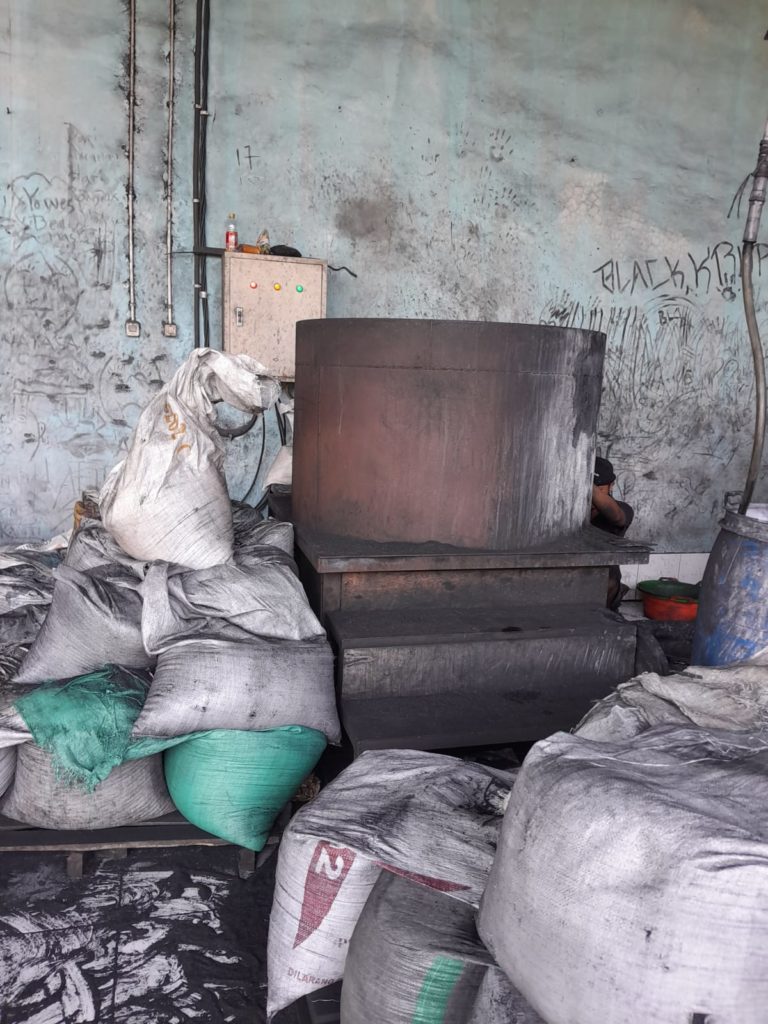
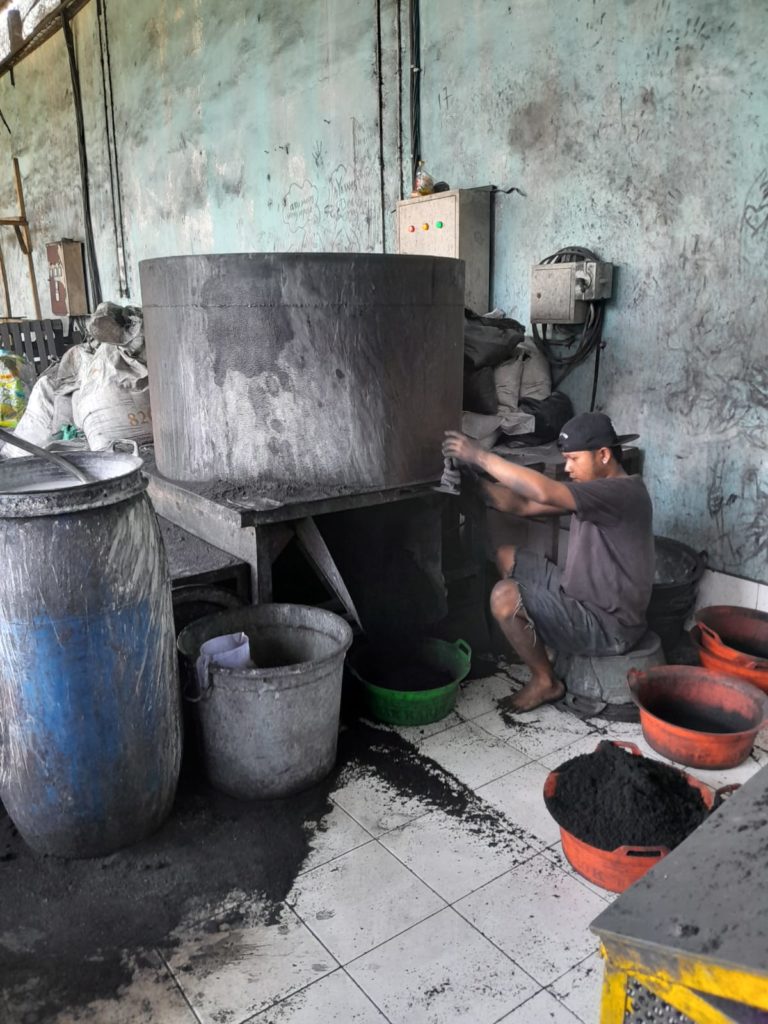
In the mixing process, charcoal is mixed with natural adhesive (tapioca flour) as much as 5% of the amount of Charcoal Flour, and enough water.
5. Blending Process
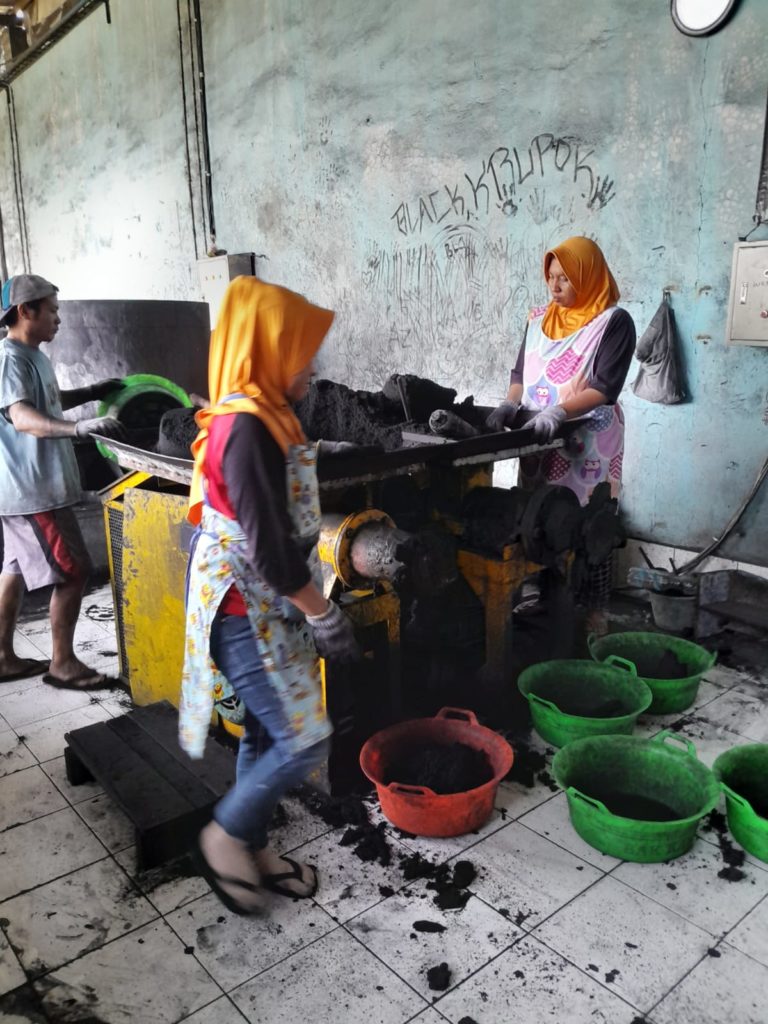
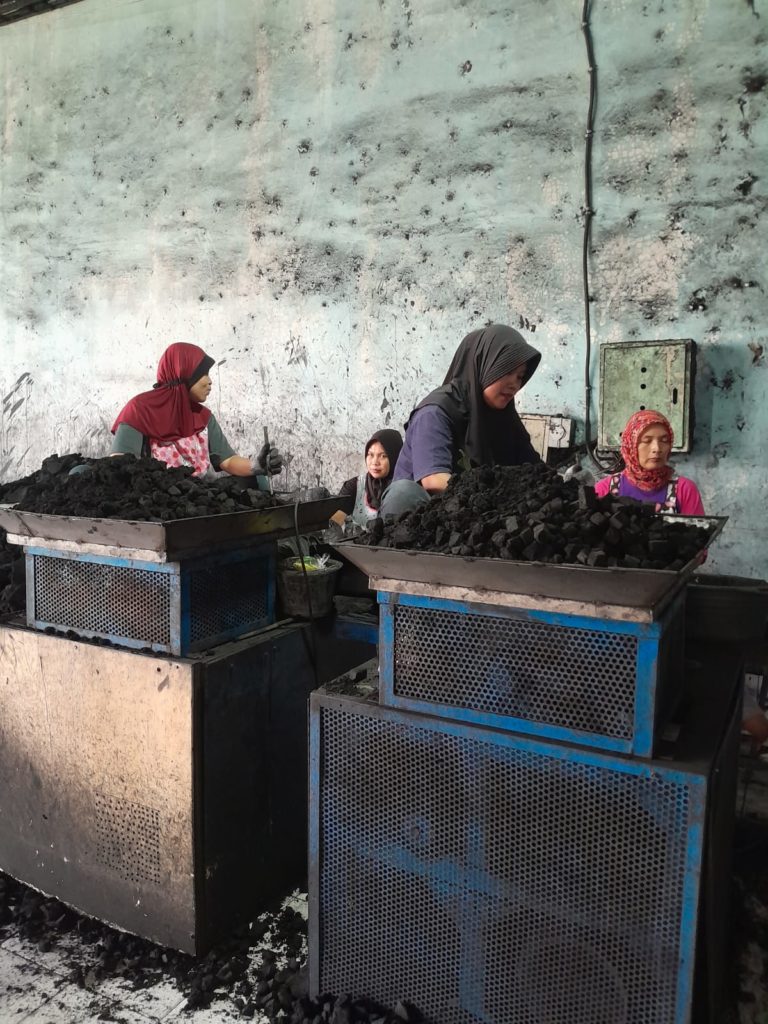
The blending process is a compaction process that is carried out in 2 stages so that the charcoal dough is more even and solid.
6. Cooling Process (After Blending)

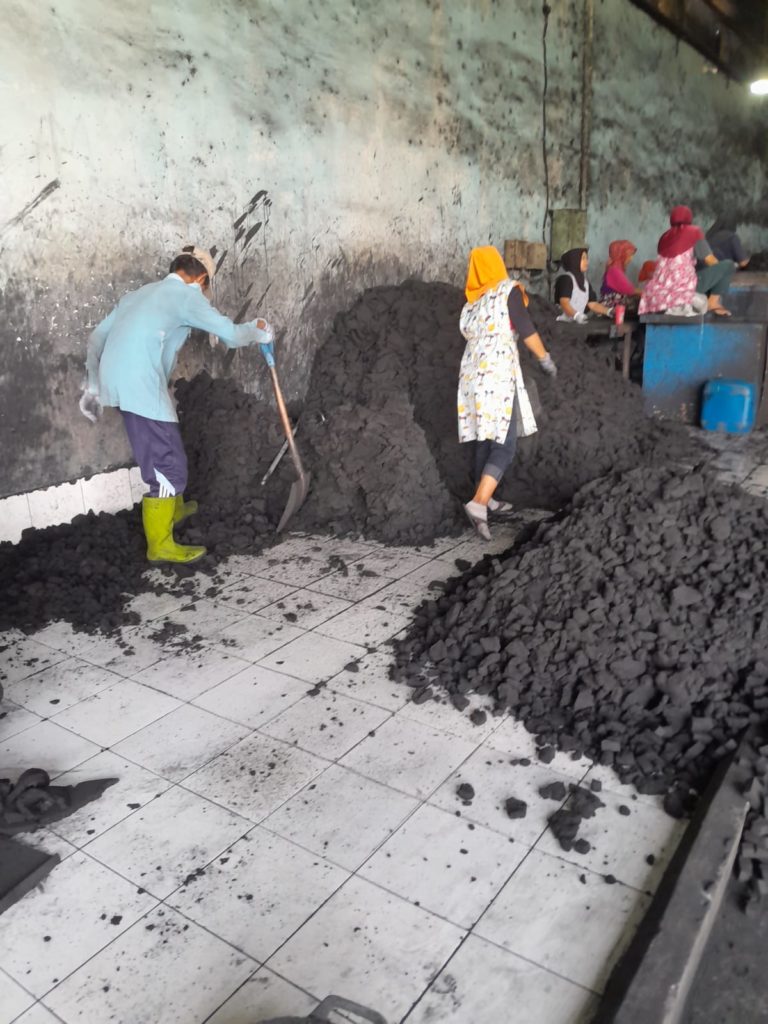
After the blending process, the dough is left to stand for ± 24 hours to ensure that the adhesive on the dough binds perfectly.
7. Molding and Cutting
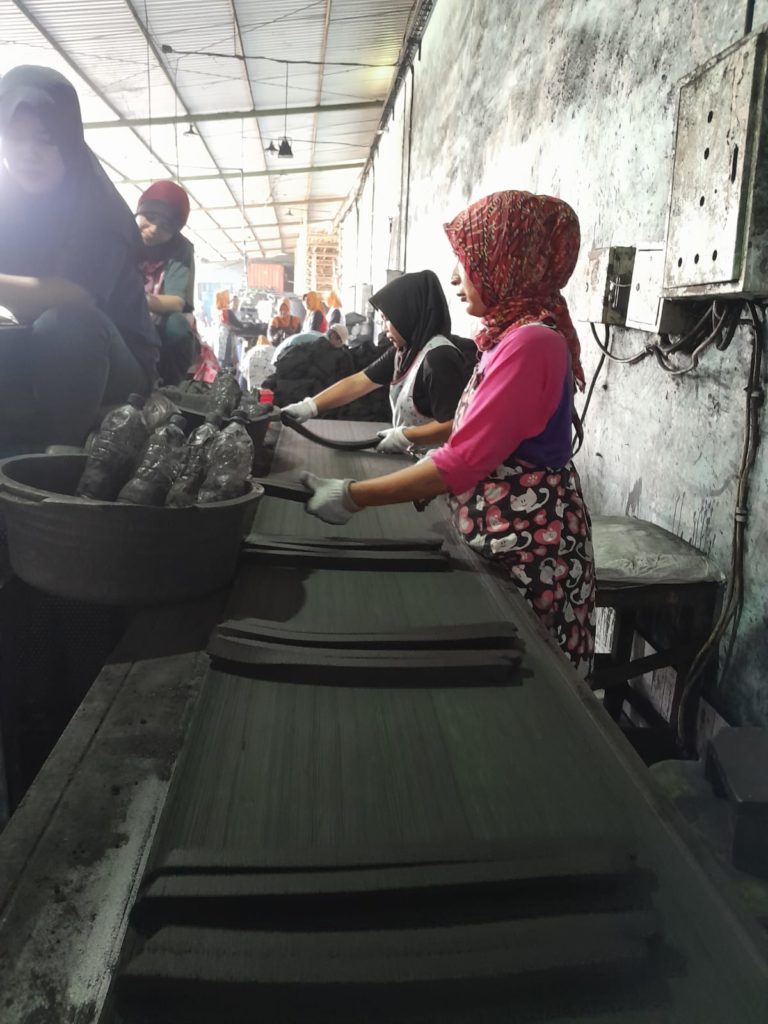
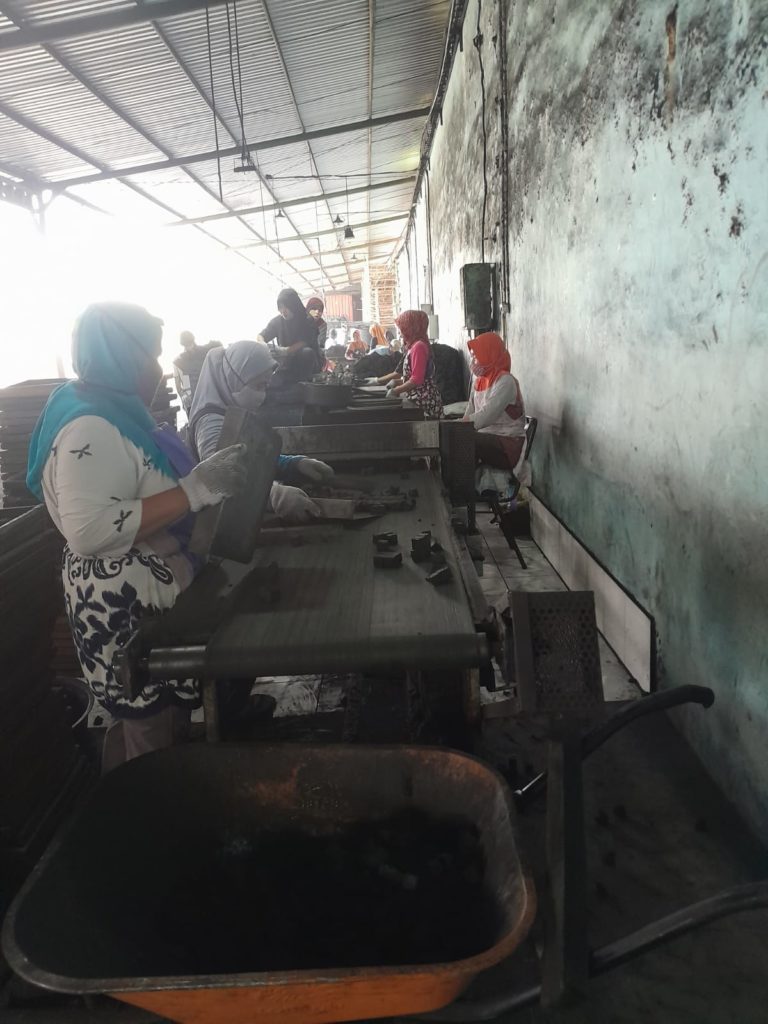
The dough that is already smooth and solid is then printed and cut using the In Line Cutting method with the size specifications stated in the Work Order (WO).
8. Drying Oven Process
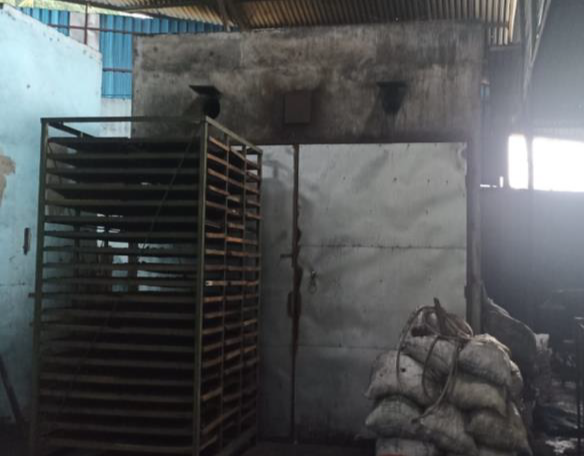
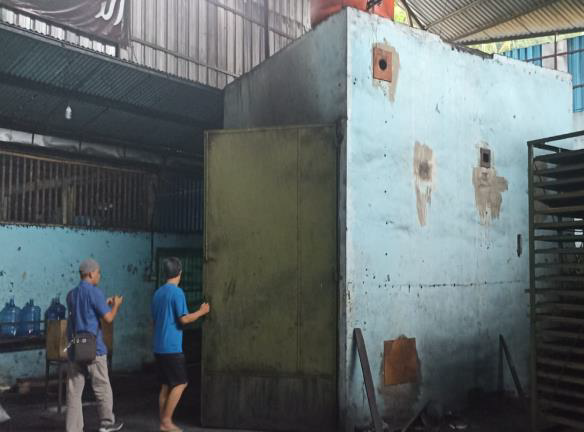
The drying process uses a dryer / oven for 30 hours (depending on the size of the molding) with a maximum temperature of 100℃.
9. Final Inspection
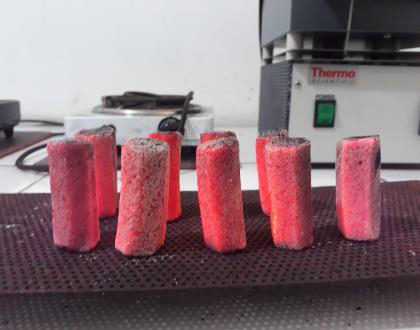
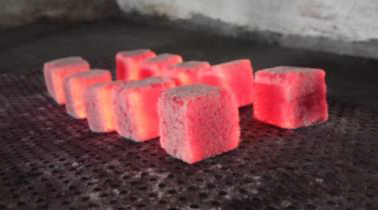
After leaving the oven, the final inspection process will be carried out in several tests with several test parameters.
10. Cooling and Weathering Process
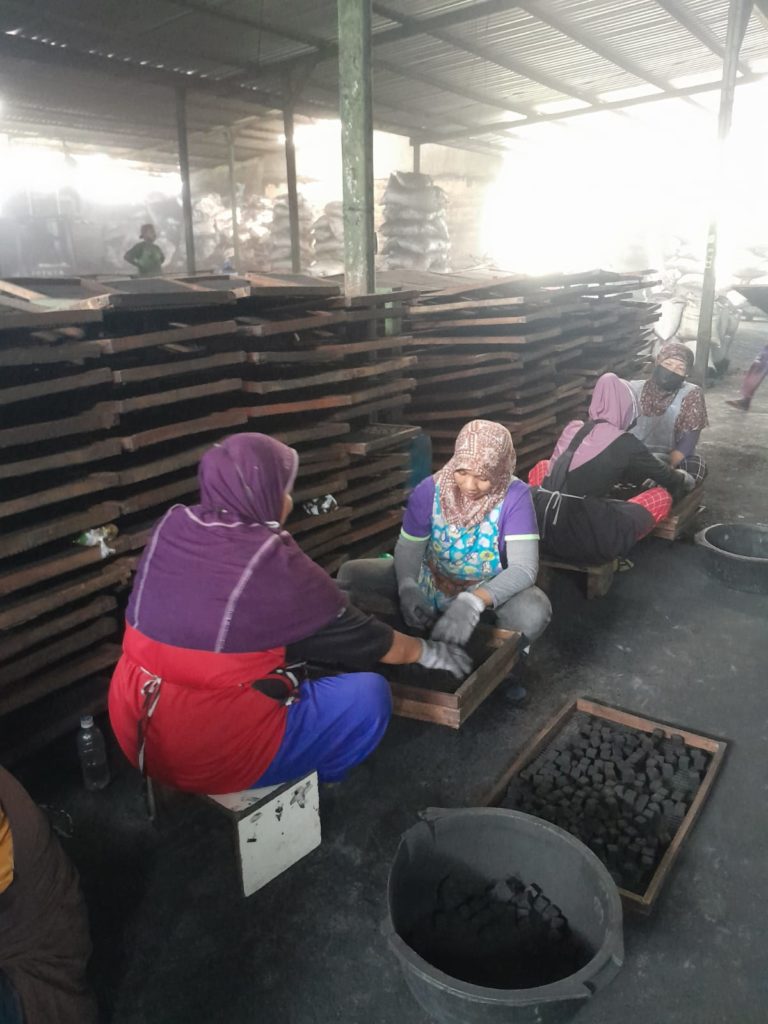
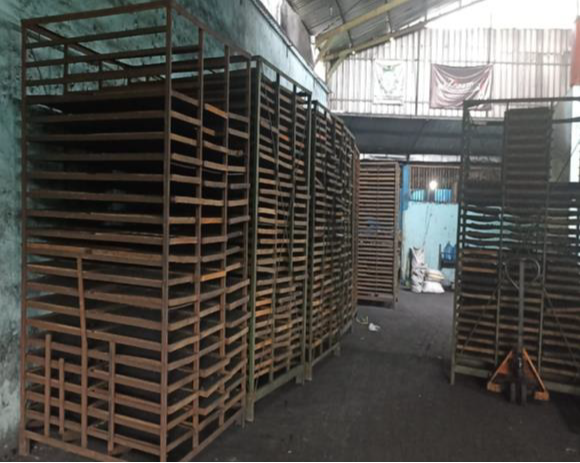
After taking out the product from the oven, cooling and weathering process is performed and takes at least 14 days, that covers placing in the racks, putting in the temporary sacks, final packing and storage.
11. Packaging Process
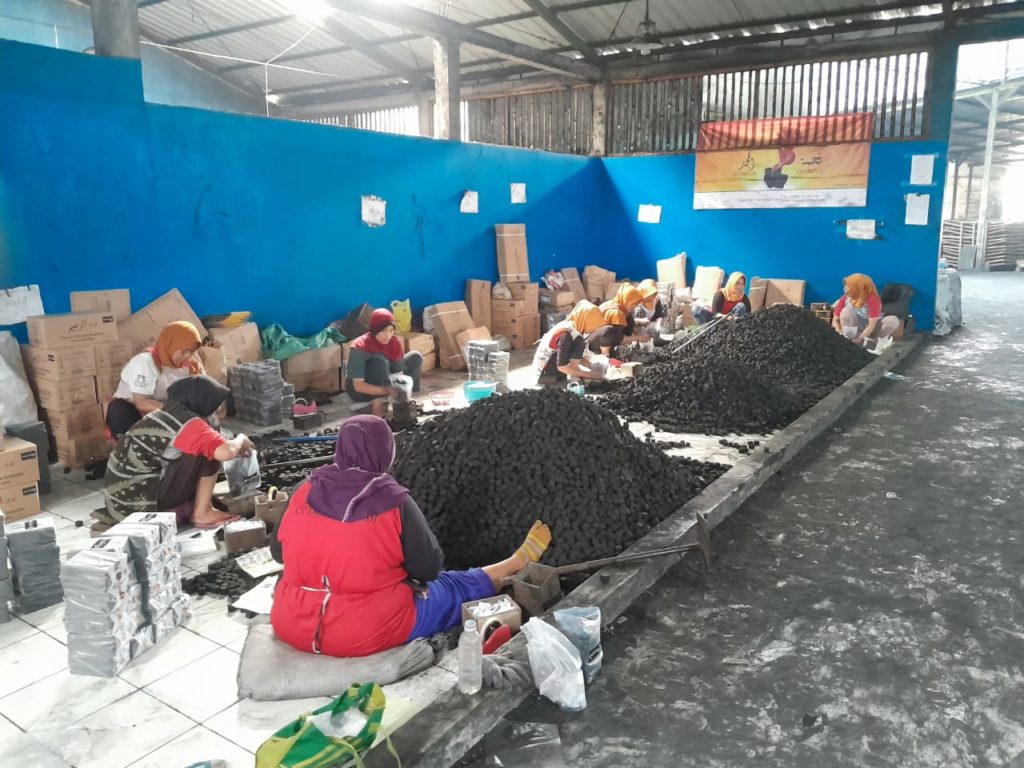
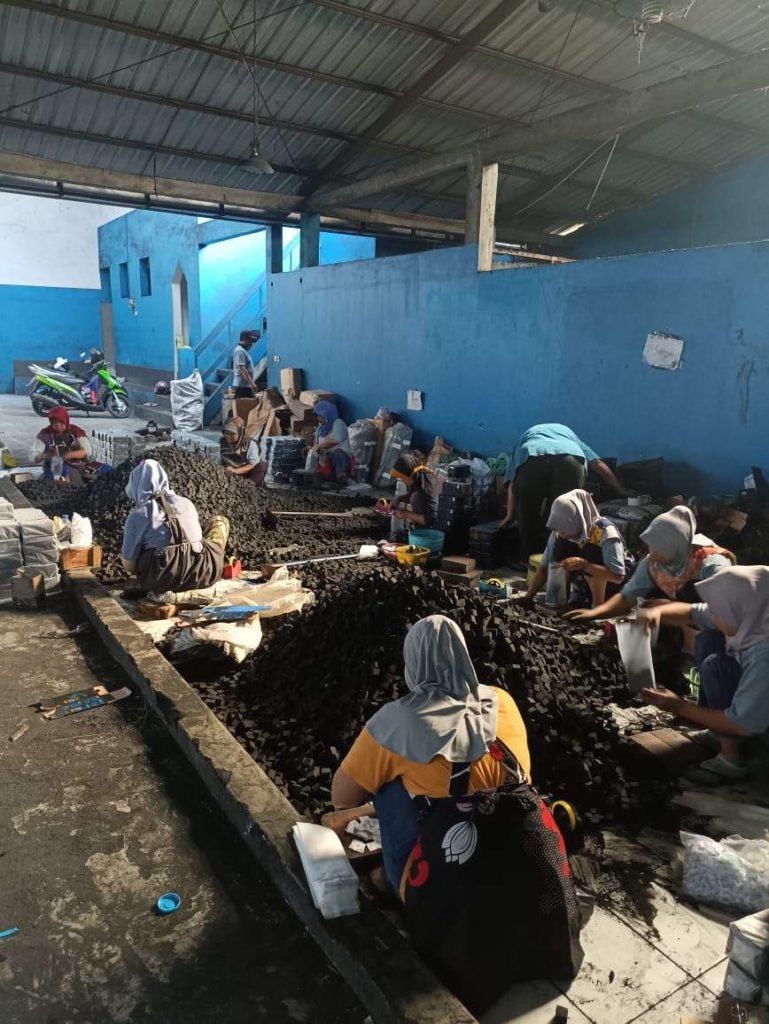
All shapes & sizes of finished product packaging (inner plastic, inner box, and master box) are adjusted to the existing Work Order.
12. Storage
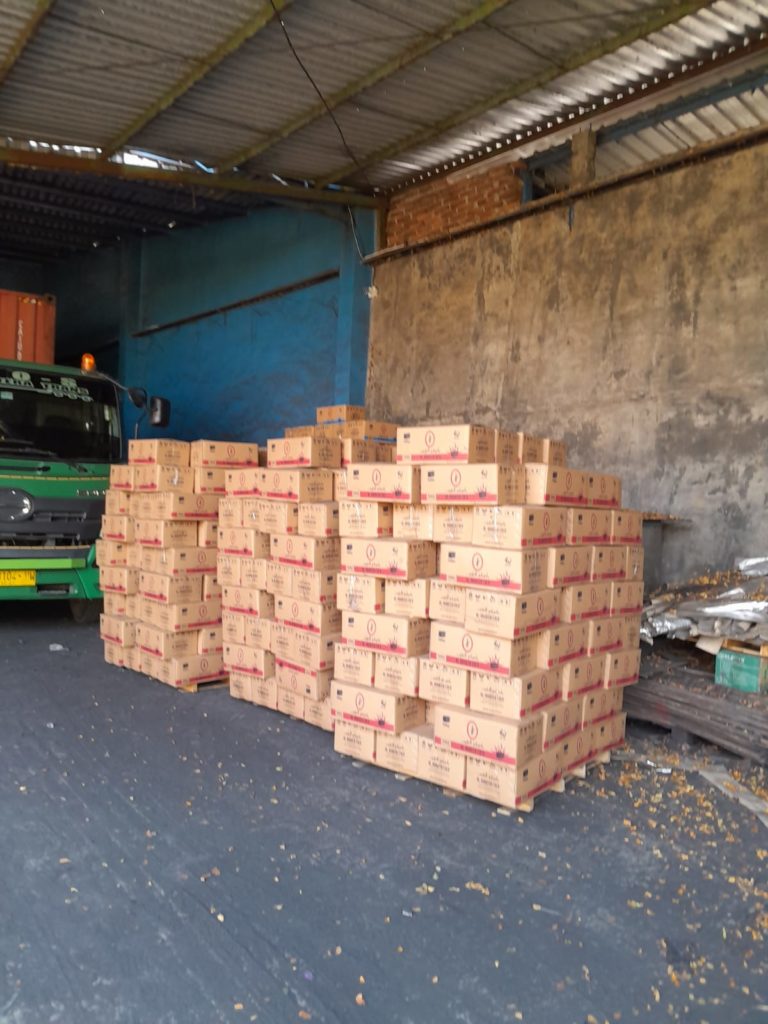
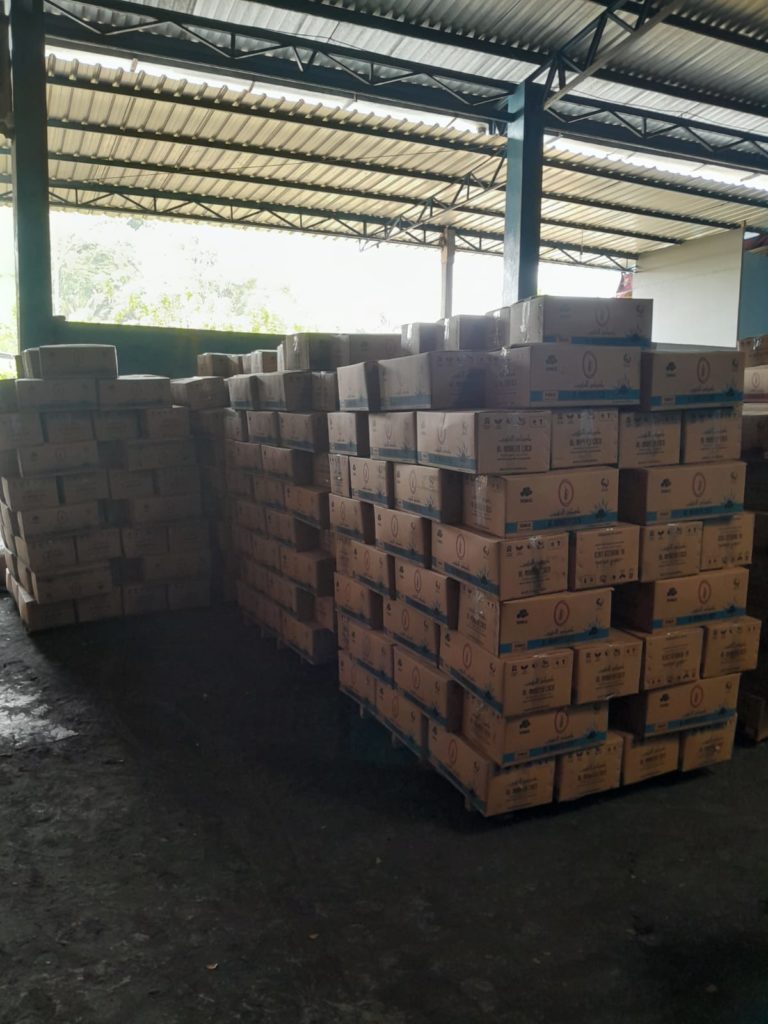
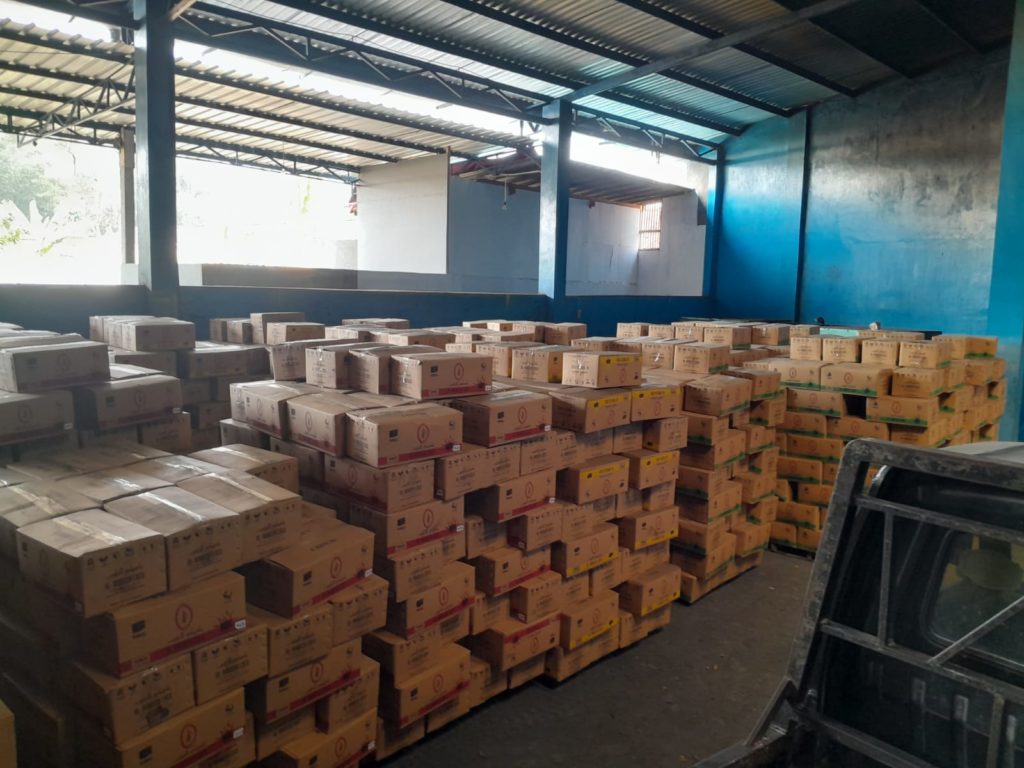
The final product is stored stacked on pallets to avoid contamination.
OUR SHIPMENT
Our company specializes in manufacturing high-quality briquettes and ensuring their safe and efficient delivery to customers across Europe, the Middle East, Africa, Asia, Australia, and America.
To safeguard the integrity of our products during transportation, we employ a meticulous process that includes containerization and the use of safety nets.
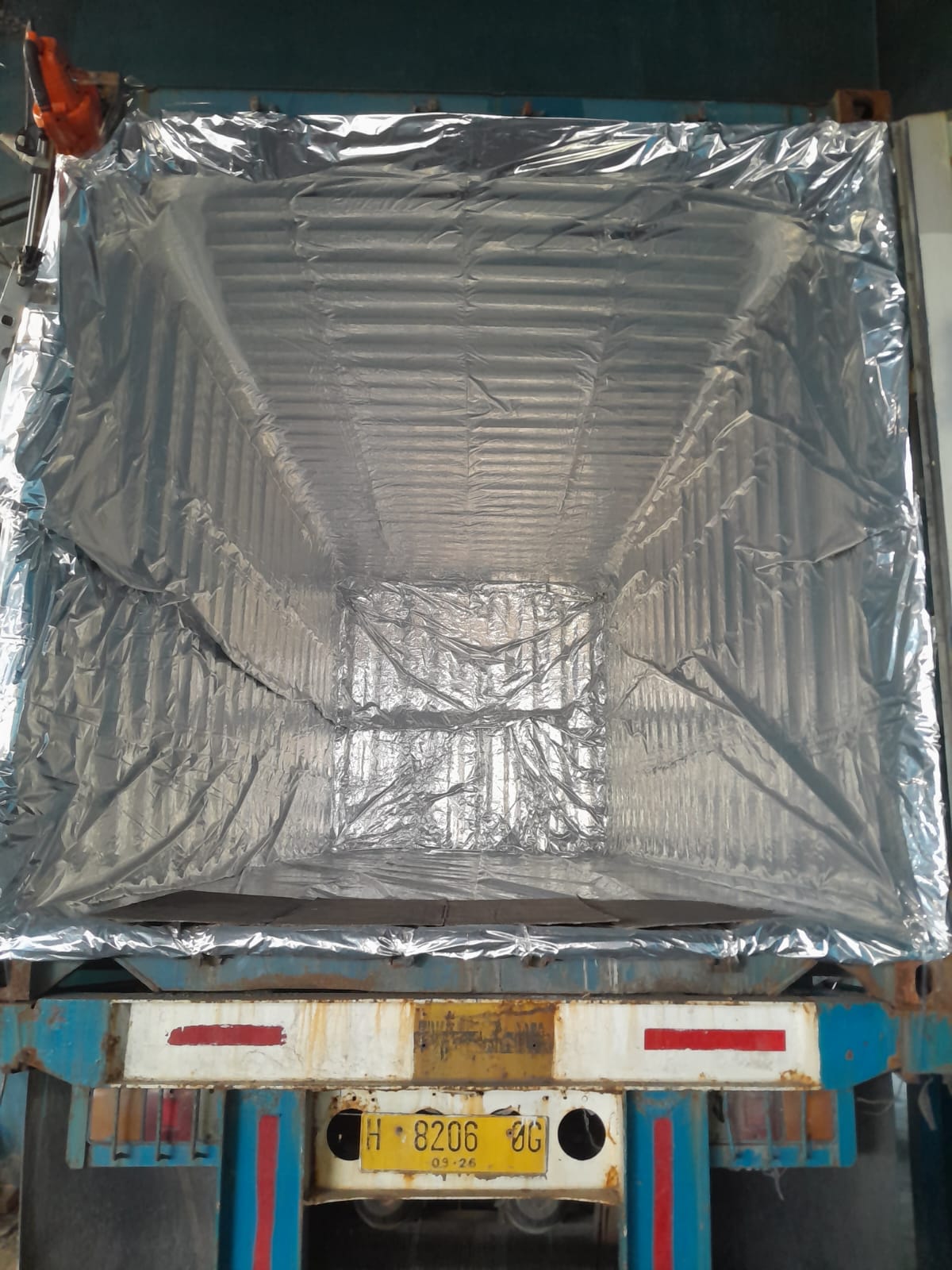
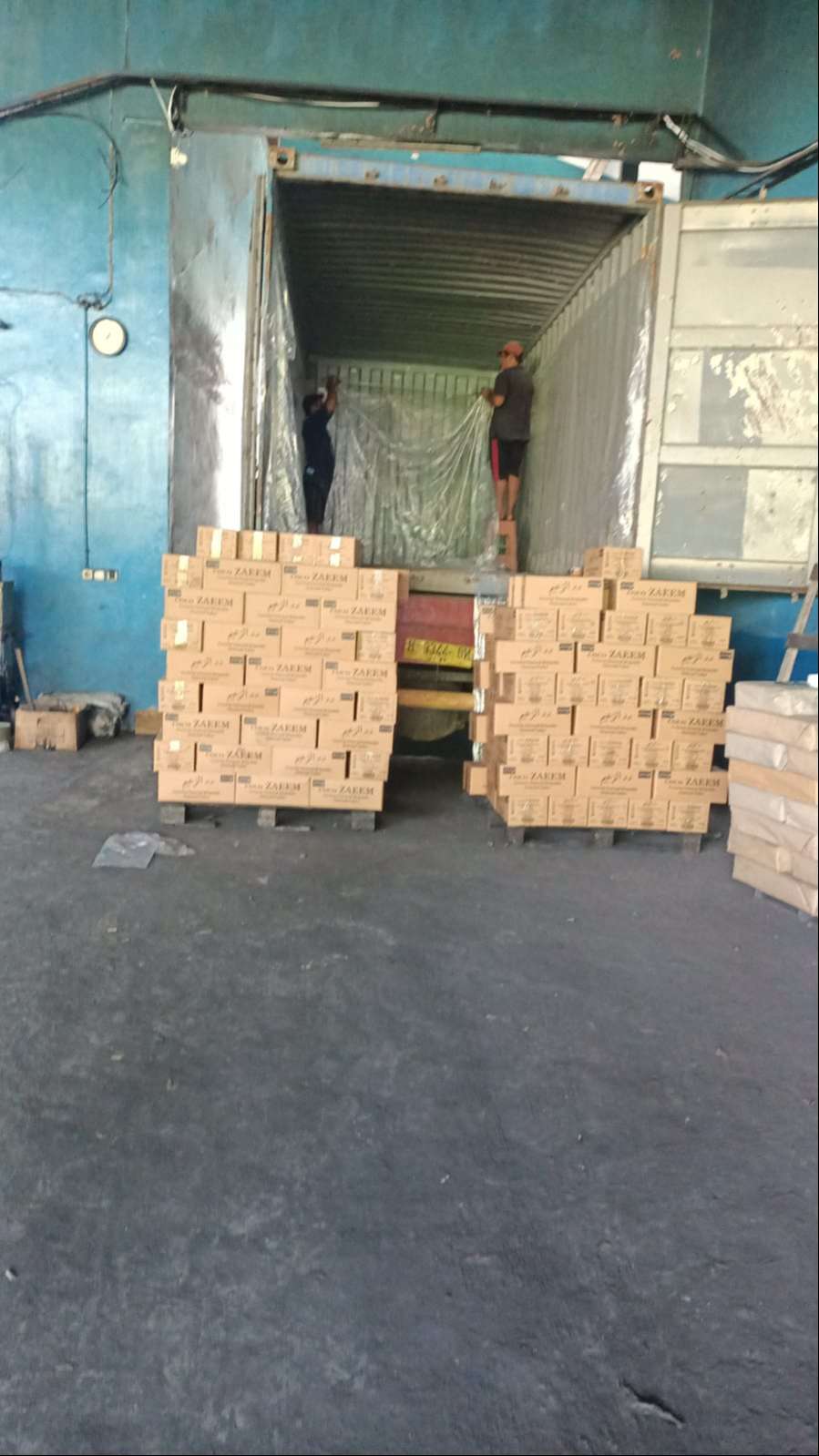
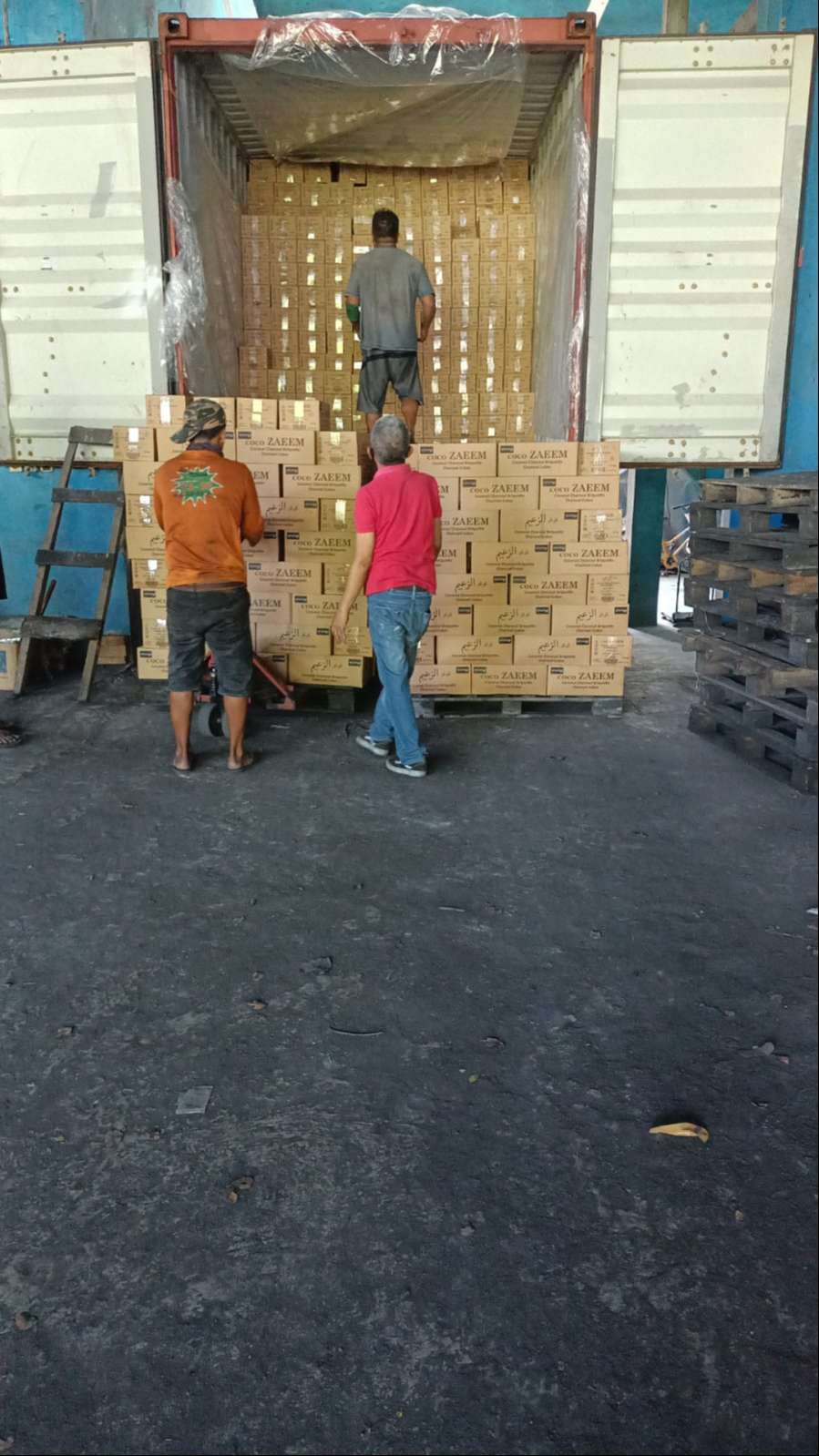
Our briquette shipment process is designed with precision and care to ensure that our products arrive safely and in pristine condition at destinations worldwide. The combination of containerization and safety net coating guarantees the security and quality of our briquettes, allowing us to serve our global clientele effectively and responsibly.
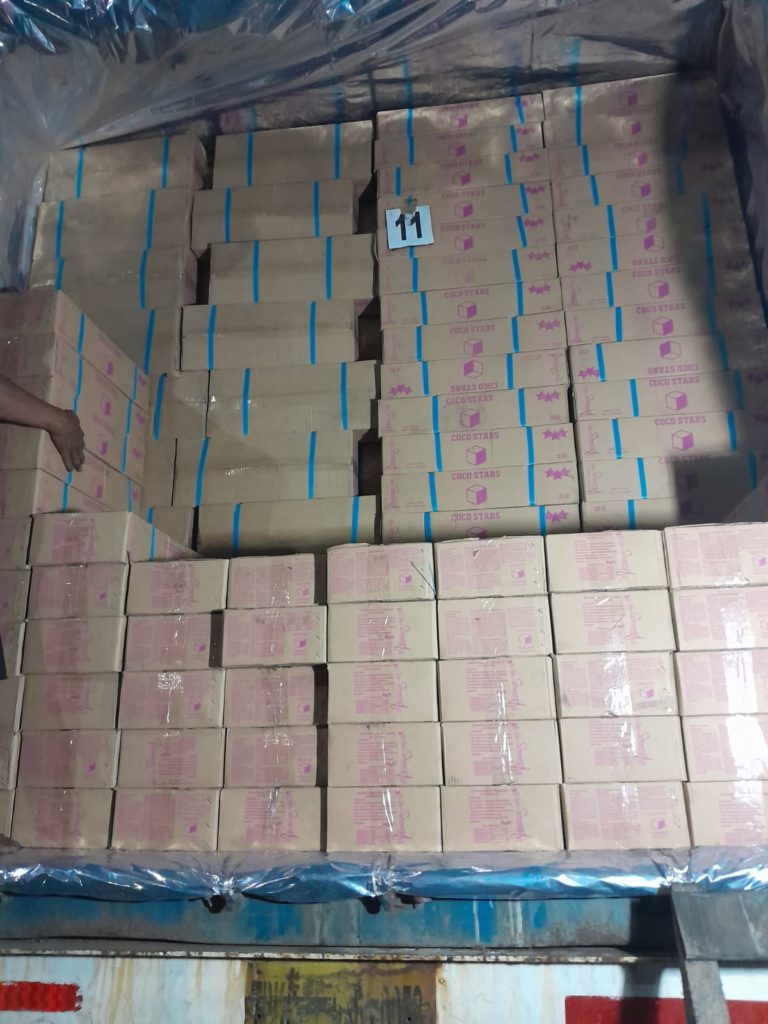
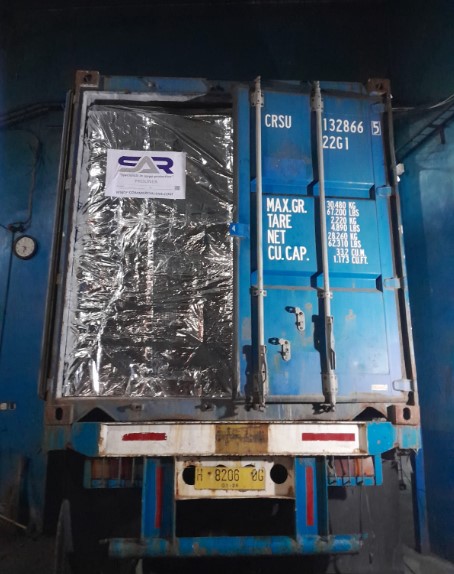
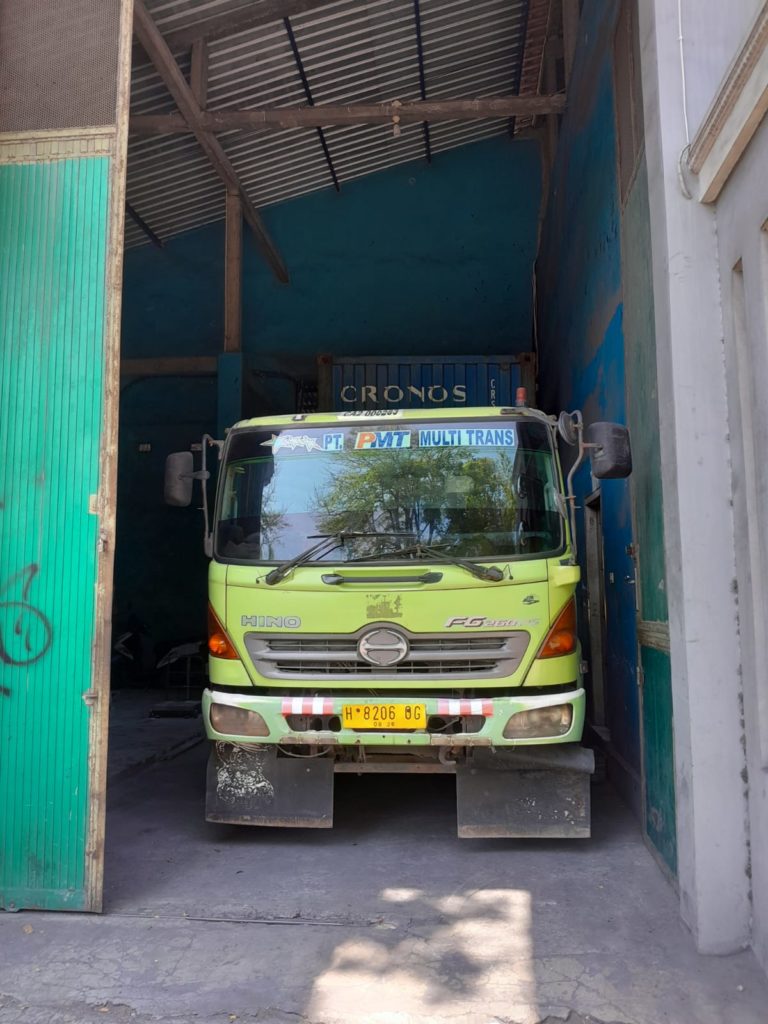